In the maze of modern technology, metal electrical panels and enclosures are the silent guardians. They aren’t just components; they’re the heartbeat of electrical systems across the globe, keeping our industries, homes, and businesses safely powered. But have you ever stopped to think about the journey these panels take from concept to reality? Let’s delve deeper into the process — it’s likely more complex than you imagined!
From Drawings to Reality: The Initial Sketches
The creation of an electrical panel or box starts with a vision—a detailed technical drawing. This is where the magic begins and the first spark of innovation ignites. Engineers and designers team up, meticulously pouring over plans to ensure that every electrical requirement is met with unparalleled precision, all the while adhering to the strictest safety standards. They carefully consider the panel’s future home, whether it be in the harsh conditions of an industrial site or the controlled atmosphere of a data center, anticipating the challenges it might face. The team also deliberates on the panel’s layout, the integration of components such as circuit breakers and connectors, and the pathways for wiring, ensuring that the design accommodates all the vital internals it will safeguard.
This phase is not just about meeting current needs but also about foreseeing future advancements and requirements, ensuring that each panel is not only fit for its immediate purpose but also adaptable for emerging technologies. This is when the foundation is laid for a product that embodies both form and function, setting the stage for the meticulous fabrication process that follows.
Choosing the Right Shield: Material Matters
Selecting the appropriate material is a pivotal step in the fabrication of a metal electrical panel, box or enclosure, as the chosen material acts as the product’s first and most crucial line of defense. The decision typically narrows down to high-grade steel or aluminum, both prized for their exceptional toughness, inherent rust resistance, and unparalleled ability to withstand the harshest environmental conditions, from extreme temperatures to corrosive atmospheres. Choosing between the two means evaluating the specific demands of the panel’s operational environment, the expected mechanical stresses, and potential exposure to chemicals or moisture. Additionally, sustainability and recyclability of materials are increasingly becoming important factors in material selection, aligning with global efforts towards environmental responsibility. This careful selection process ensures not only the longevity of the panel and the protection of its internal components but also contributes to the overall reliability and safety of the electrical systems they serve. By prioritizing material quality and suitability, the foundation for a durable, efficient, and safe electrical panel is firmly established.
Crafting Perfection: The Art and Science of Fabrication
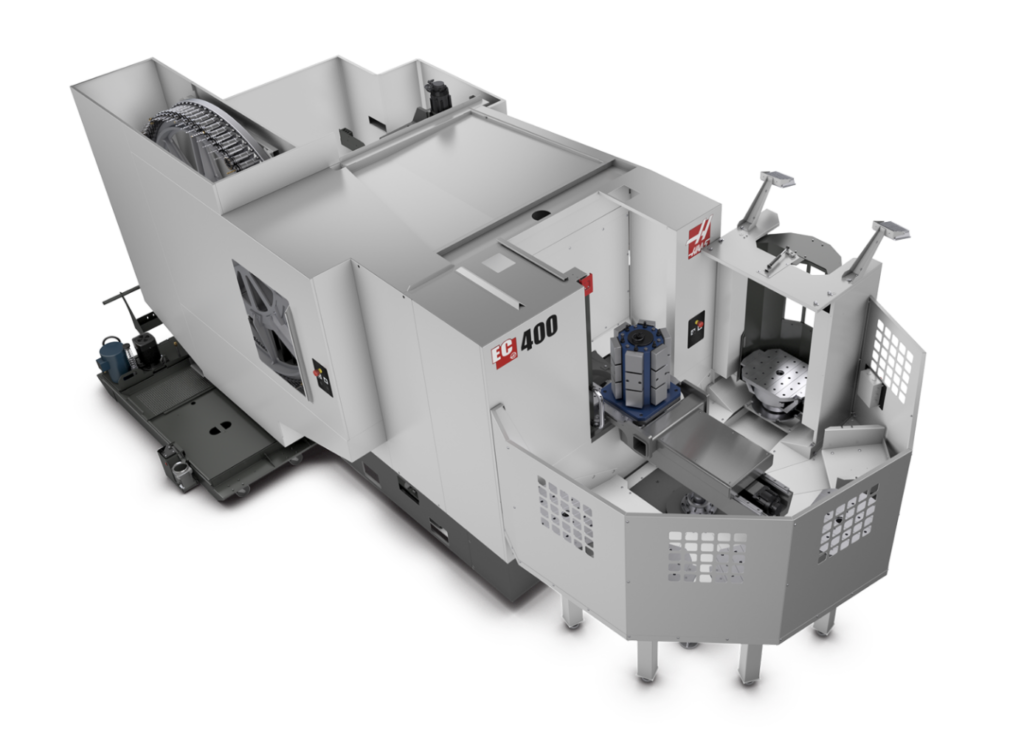
Once the plans are set and the ideal materials chosen, the fabrication process transitions into a phase where the precision of modern machinery take the spotlight. CNC (Computer Numerical Control) machining stations and advanced laser cutting equipment become the primary tools, wielding their technological prowess to cut and shape metal with unparalleled accuracy. This phase is more than just crucial—it’s where the envisioned design begins to take physical form. Every piece cut and shaped during this stage must fit flawlessly, ensuring that the final assembly results in a panel that embodies both strength and precision.
Additionally, the use of software-driven machinery allows for adjustments on the fly, accommodating any last-minute design changes or optimizations. This synergy between advanced technology and skilled human oversight ensures that the fabrication process not only meets the required specifications but often exceeds expectations, setting the stage for the next steps in the creation of a robust and reliable metal electrical panel.
Piece by Piece: Putting it All Together with Assembly and Integration
Now, the individual components come together during the assembly and integration phase. Circuit breakers, busbars, wiring, and other crucial elements are meticulously placed and secured by technicians who are not just skilled in the art of assembly but are also masters of integration. This phase goes beyond simply putting parts together; it involves a strategic orchestration of components to ensure seamless functionality and efficiency. The technicians’ expertise in understanding the relationships between different parts plays a pivotal role. They ensure that every piece not only aligns perfectly with the initial designs but also works in concert with the others to achieve optimal electrical performance. This step is a testament to precision, attention to detail, and a deep understanding of electrical systems, underscoring the importance of both mechanical fit and electrical harmony. The integration process ensures that the assembled enclosure functions as a cohesive unit, ready to serve its purpose effectively, marking a critical point where design transitions into tangible utility.
The Final Touches: From Welding to Surface Finishing
In the fabrication process, welding is the pivotal moment where multiple parts are carefully fused into a unified, robust enclosure. This step goes beyond simply metal joining; it’s more like forging a fortress, ensuring structural integrity and resilience. Following welding, each panel undergoes a thorough smoothing to eliminate any rough edges, and a comprehensive cleaning to ensure a pristine surface, setting the stage for the final transformation.
The application of powder coat then usually follows, a process that not only enhances the panel’s aesthetic appeal but also serves as a formidable protective shield against the elements. Automated powder coating uses electrostatically charged particles to ensure an even, durable outer layer that adheres to the metal surface more effectively than traditional paint. The result is a finish that offers enhanced durability, resistance to corrosion, chipping, fading, and scratching, effectively extending the lifespan of the panel. Moreover, this eco-friendly process emits fewer volatile organic compounds (VOCs), making it a preferable option for both the environment and workplace safety. Through these meticulous final touches, each panel is armored and beautified, ready to withstand the rigors of its operational environment while maintaining its aesthetic integrity.
Ensuring Perfection: The Rigors of Quality Control
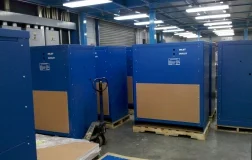
All orders must pass through stringent quality control assessments before they can be shipped to the end customer. This rigorous, multi-stage process subjects the panels to a battery of tests designed to validate adherence to the highest safety and performance standards. It’s a holistic assessment that goes beyond simple checks, rigorously evaluating structural integrity to ensure each weld holds firm under pressure, testing electrical functionality to guarantee reliable performance under operational loads, and assessing resilience to affirm the panel’s ability to withstand conditions such as moisture, temperature extremes, and chemical exposure.
This examination also includes checks for compliance with industry regulations and certifications, ensuring that each product not only meets but often exceeds the required benchmarks. Through this exhaustive QC process, EVS Metal commits to delivering panels and enclosures that are not only functionally sound and safe but are also durable and dependable, ready to perform as required once installed in the real world. This unwavering dedication to quality underscores EVS Metal’s reputation for excellence and reliability in the metal fabrication industry.
The Bigger Picture: The Essential Role of Metal Electrical Panels
Metal electrical panels play a pivotal role as some of the unsung heroes of our infrastructure, orchestrating the flow of electricity to power our industries, illuminate our homes, and energize our daily lives. These panels and the enclosures that they form do much more than distribute power; they ensure the safety and reliability of electrical systems, protecting against overloads and short circuits that could lead to equipment damage or catastrophic failures. By managing electrical loads and providing a centralized control point, they facilitate maintenance and troubleshooting, thereby minimizing downtime and enhancing productivity across various sectors. Whether hidden within the walls of our homes or at the heart of a sprawling industrial complex, their usefulness is undeniable. They might operate behind the scenes, but their role is fundamental in maintaining the rhythm of our modern world, ensuring that electricity—a cornerstone of contemporary life—flows safely and reliably to where it’s needed most.
Behind the Scenes: Why Electrical Panels and Enclosures Matter
The journey of fabricating an electrical panel is a fascinating blend of innovation, precision, and craftsmanship. It showcases the combination of cutting-edge technology and meticulous manual skill emblematic of engineering and manufacturing excellence. As our reliance on electricity continues to grow, their importance has never been greater, because this process isn’t just about creating a product; it’s about powering the future, one enclosure at a time.